QUALITY IMPROVEMENT – Engineer & Consultant Services
WE HELP Manufacturing Companies with Quality Improvement Engineering & Quality Awareness We Can Help Improve Processes and Reduce Costs
.
“If You Don’t Have Quality – You Won’t Have Customers“
.
WHY IS QUALITY IMPORTANT IN MANUFACTURING and in BUSINESS:
- You realise that there is nothing worse than bad service.
- It takes a long time to get a customer
- But ONE mistake to lose them.
CUSTOMERS EXPECT QUALITY – NOT Once, but every-time – Quality is the key to your customers satisfaction… And you need customers for the growth of your company…
.
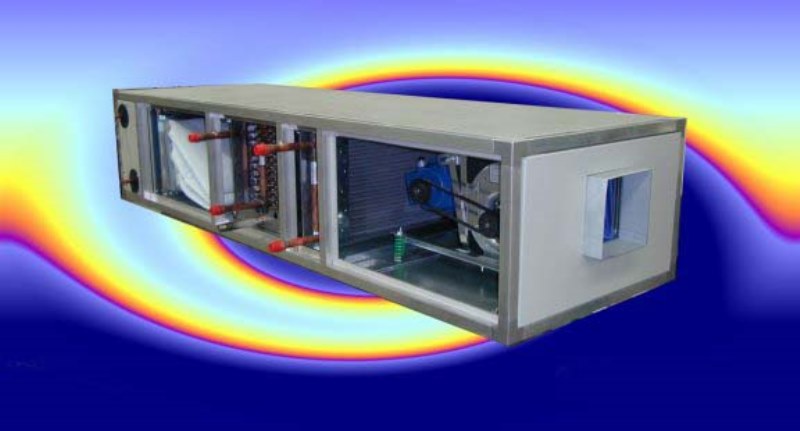
Customers Want:
- 1.RIGHT PRICE
- 2.QUALITY at 100%
- 3.BEST SERVICE at 100%
- 4.DELIVERY When the Customer Wants It
.

Commitment To Quality:
- Design OUT Possible Rejects
- Design OUT Complicated Designs
- Design OUT a Complicated Process
- Design IN Standardisation of Product
- Design IN Simple Quality Awareness Procedures
- Design IN Simple Processes to Reduce the Electric Bill
.
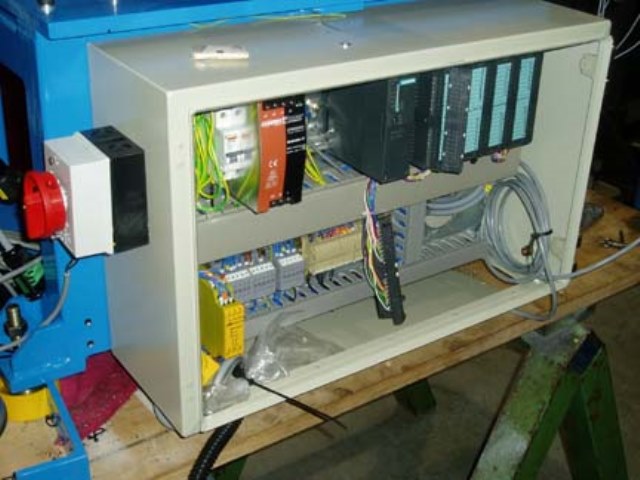
Company Benefits:
- Reduced Rejects and Scrap
- Reduced Having To Remake Product
- Reduced Wasting Time and Energy Costs
- Reduced Land-fill and Increased Cash-Flow
- Improved Business and Future Growth
.
Edwards Deming said:-
Adopt The New Philosophy:
- Design products and services to meet customers’ needs.
- Put your customers’ needs first, rather than to competitive pressure.
- Look at how the process is carried out – Not just numerical targets.
- Provide support and resources so that production levels and quality are achievable.
- Create your “Quality Vision” and implement it – “Fit For Purpose” not cheap and nasty.
- KEEP IT SIMPLE – REDUCE VARIATION – INCREASE PRODUCTION – INCREASE SALES
.
Services We Offer:
.
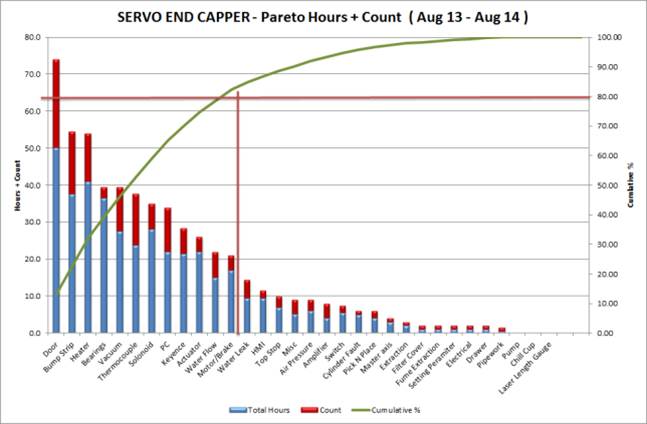
Simple Quality Improvement Implementation:
Together we can help you achieve “Right First Time – Every Time”
- The First Step: in improving quality – reducing rejects – reducing costs… IS Identify & Analyse Root Cause of quality issues, customer complaints, supplier issues and “human errors”
- The Second Step: is to put Quality Standards and Quality Awareness Procedures into place
.
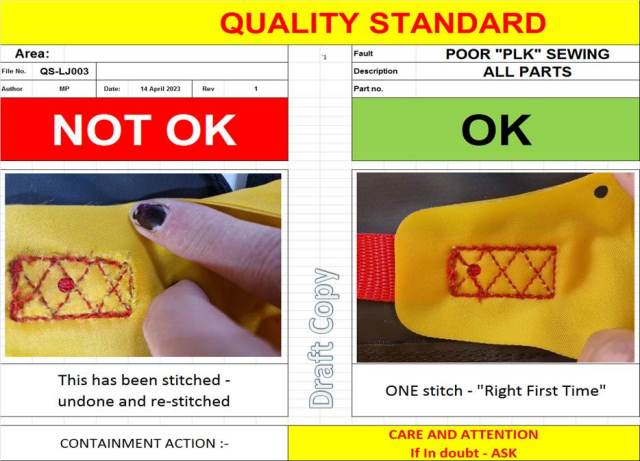
Quality Improvement Procedures:
It is generally understood in management circles that if an instruction is written – Then everyone will understand them – “This Is Not True”
- Many procedures are “mis-read, not understood or even none existent”
- Temporary staff are expected to “do the job” and get the product quality right first time, without first being trained “This does not happen”
- Procedures need to be SIMPLE – in SIMPLE ENGLISH to be understood
.
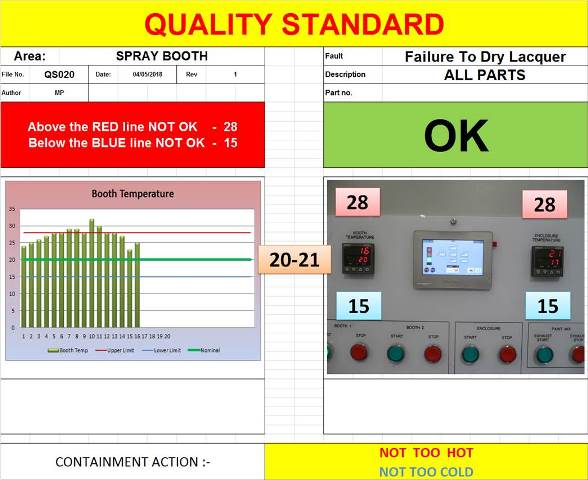
Quality Procedures In Manufacturing: THE KEY TO QUALITY
- Standard Op Procedures – improve operator performance & quality.
- Quality Awareness and SOPs – eradicate manufacturing issues
- With Operator Training – you eradicate rejects and re-makes
- With a 100% quality product you will retain customer satisfaction
- Management know what the customer wants – But does the workforce?
- We Write Quality Procedures – Eradicate NCRs and “Human Error”
.
We are that “independent extra pair of eyes” with 30+ years experience and knowledge
We help people in business build a better business
.
Quality IS The KEY to a Better Business and Your Future
.
Atherton Management Services Ltd
.
Please Contact Us, We Are Happy To Help:
We’ve generated for our clients between £50k and £2.0M per project
For over 30 years we’ve designed and implemented “Business Improvement” Projects.
Please Contact Us, tell us your issues – tell us how you would like to improve your business.
Please Contact Us:- UK – 07300 788 486 – or by E-Mail