Process & Production Improvement Project In Manufacturing
How To Improve Process & Reduce Costs in the Clothing Manufacturing Workplace – Case Study Implemented
.
Case Study Implemented – Clothing Manufacture: Factory Organisation
OBJECTIVES:– To raise all standards – engage the workforce towards quality “Right-First-Time” RESULTS:- To de-clutter stores – re-engineer layout – Improve efficiency, overall yield circa 30%
.
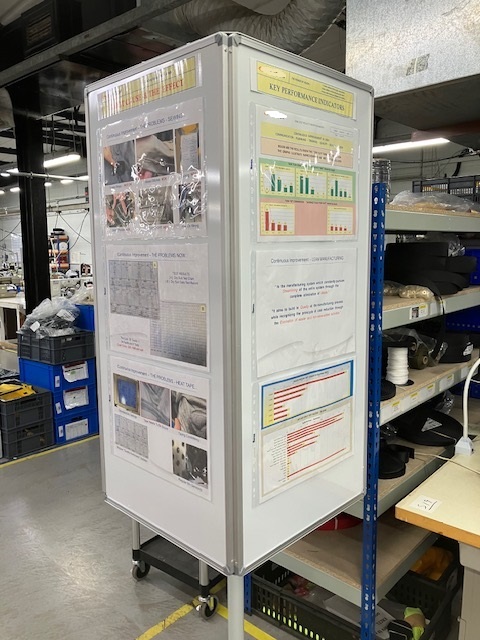
PROJECT WORK DONE:
- 1.Listen to the client
- 2.Draw present state factory layout
- 3.Re-engineer to a LEAN floor layout
- 4.The introduction of Section Kitting Areas
- 5.The introduction of Daily Production Targets.
- 6.Stores organisation to include 7S – Kanban – Min/Max levels
- 7.The sourcing of materials and “on time delivery from suppliers”
- 8.Root Cause Analysis of all process issues including test and quality
- 9.Value Stream Mapping of Process and Reduction of Non-Value Waste
- 10.Continuous Improvement Planning for Future Projects
- 11.The Introduction of Quality Awareness Procedures
- 12.Operator Training and Quality Awareness
.
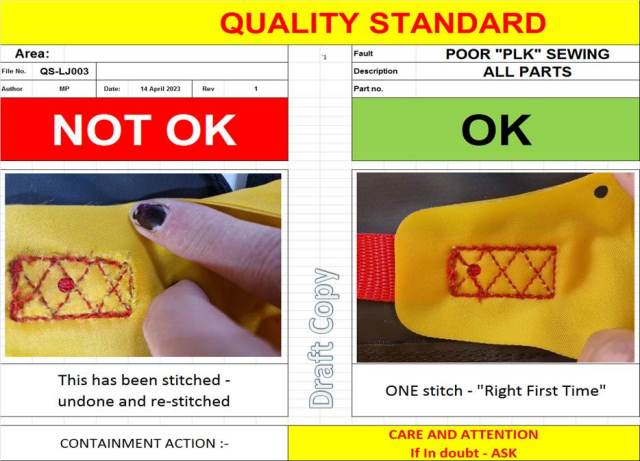
PROJECT RESULTS:
- Process Improvement
- Production Improvement
- Product Quality Improvement
- Improved Product Throughput
- Stores and Inventory Organisation
- Sales and Business Growth Potential
FINANCIAL BENEFITS:
Process improvement that was implemented would generate circa 30% production improvement. Also could produce an extra £2M in sales revenue.
.
We Help People Identify Opportunities for Improving Business and Implement Change
.
Atherton Management Services Ltd
.
Please Contact Us, We Are Happy To Help:
We’ve generated for our clients between £50k and £2.0M per project
For over 30 years we’ve designed and implemented “Business Improvement” Projects.
Please Contact Us, tell us your issues – tell us how you would like to improve your business.
Return On Investment; Client savings compared against contractor costs. Recent average circa R.O.I. 13 / 1
Please Contact Us:- UK – 07300 788 486 – or by E-Mail…